This research focuses on enhancing the design and assembly workflow of adaptable bending-active structures by integrating motion capture (MoCap) and extended reality (XR) technologies. Using bamboo as the primary material, we examine its elastic deformation properties and propose a workflow that enables real-time adjustments to digital models based on actual assembly conditions. Unlike traditional, unidirectional XR applications that provide only static digital guidance, our approach supports a dynamic assembly process that responds flexibly to environmental conditions through real-world data feedback.
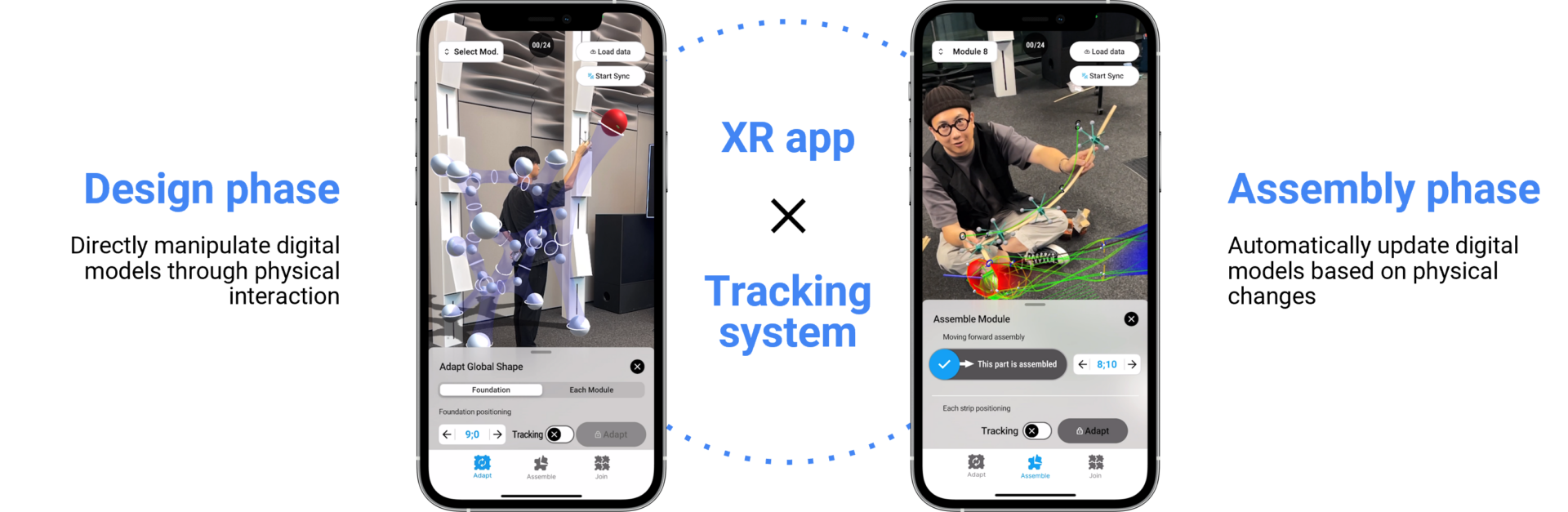
Using MoCap, we continuously track and reflect the deformation, movement, and positioning of materials, particularly during the complex assembly of modular structures. This technology merges real-world input into the digital design model, enabling immediate adjustments that improve precision and dynamically align physical and digital spaces. Specifically, we demonstrate how tracking systems facilitate adaptive shape design by detecting planes, adjusting lengths, and visualizing material bending and orientation in real-time. XR technology further allows users to interact directly with digital guides overlaid on physical components, greatly enhancing both assembly efficiency and user experience.

To improve user experience, we also designed a user interface (UI) for the XR application in MoCap. Following design guidelines from Apple and Google, we ensure a streamlined and intuitive UI that minimizes cognitive load, making the assembly workflow smoother. Through adaptive, modular workflows and real-time interactive digital modelling, this approach aims to provide assemblers with more intuitive guidance, helping them navigate complex processes and making the design and assembly of bending-active structures more adaptable and efficient.
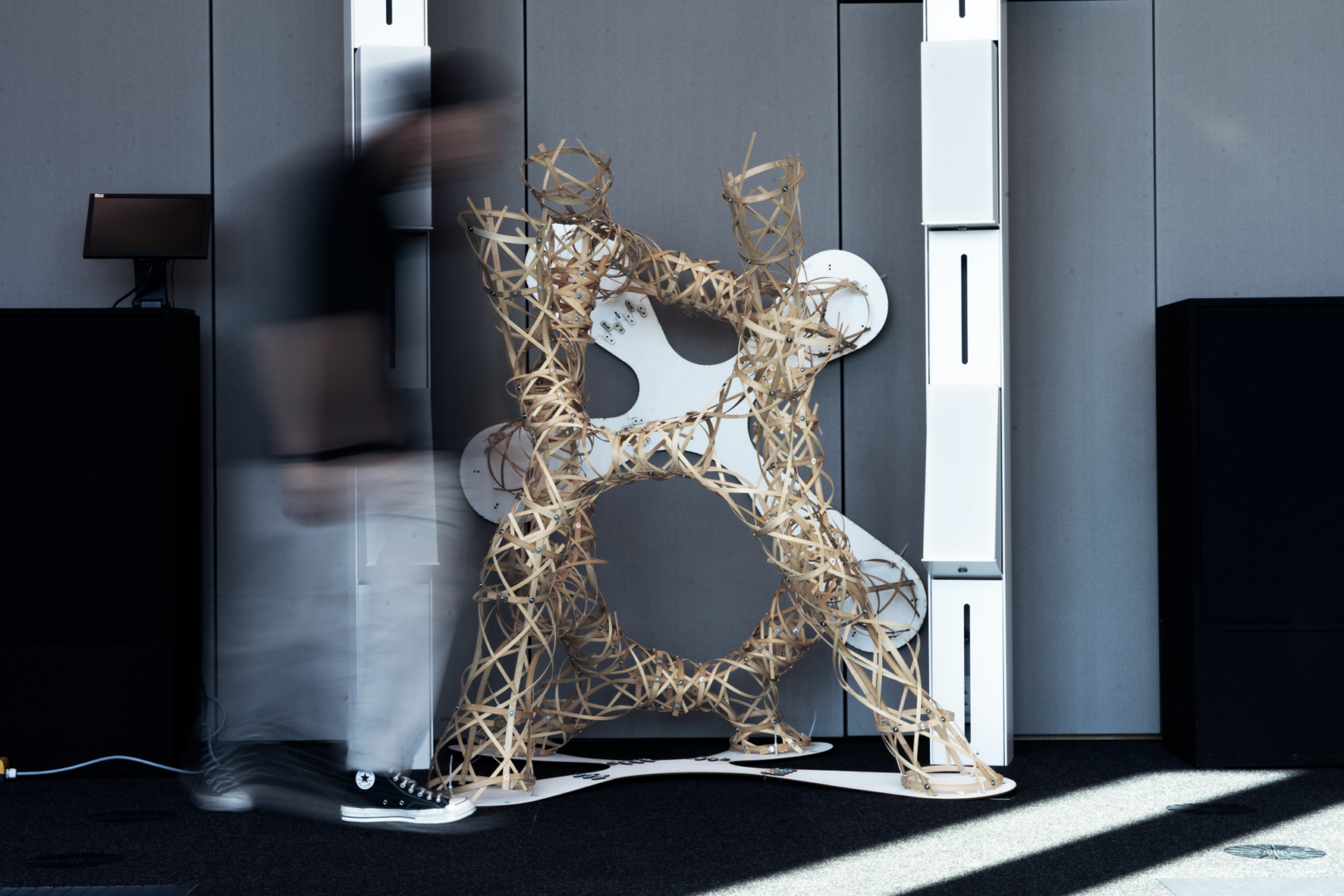
